Providing solutions to your building
McCownGordon brings strategies that create greater results.
Our Building Performance Solutions department is designed to better help our clients during preconstruction and construction. This team consists of engineers, trade partners, architects and code officials who became experts in their fields. Because this robust department has been on all sides of the table they see your project through multiple lenses. Building Performance Solutions compliments the project team and provides an unparalleled knowledge and focus.
MEP services
You need specialized individuals that know your mechanical, electrical and plumbing (MEP) systems inside and out to ensure a successful project. Our engineers are here to help make sure you are paying the right price for right-sized systems. As an owner, with our Building Performance Solution team, you’ll have a higher level of confidence your building meets your expectations.
The MEP components can be up to sixty percent of your overall project costs, so it is vital we have specialized individuals that know these systems. The team communicates heavily with the design team and reviews the drawings during preconstruction. They look for constructability issues, potential scope overlaps/gaps and options that might be more cost-effective or easier to install and maintain. With the help of the our in house engineers, our project team assembles the most accurate estimates and fills in any gaps before construction begins.
The MEP team also assists with a seamless transition during construction. The department assists with scheduling of long lead items, ensuring the MEP systems are installed properly, and provide feedback on installation time and potential man-hour requirements to help the operations team stay on track. The department continues involvement through post construction assisting with troubleshooting or any warranty items that may occur.
COMMISSIONING
By utilizing our in-house team instead of trade partners to commission a building, you’ll benefit from a more streamlined and less subjective process. Our Commissioning team serves to improve the energy efficiency of a building and reduce overall costs of operation for the owner.
Our team will already be well-acquainted with your project which makes the commissioning process seamless. Working closely with McCownGordon on commissioning during preconstruction offers owners numerous benefits, including reduced costs, fewer delays, and more sustainable and efficient designs. In addition, McCownGordon can commission already completed projects through retro-commissioning, allowing for under-performing systems to be assessed and enhanced to provide maximum efficiency.
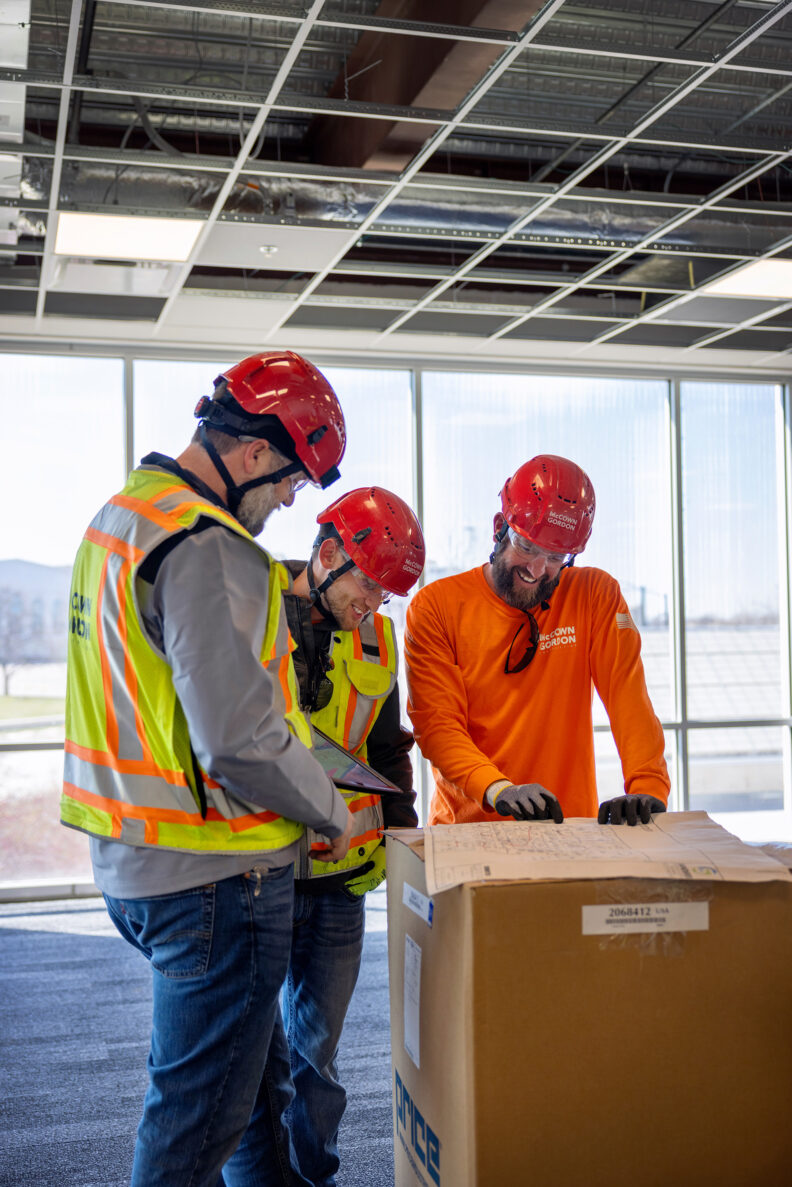
Structural and Soil
Our Structural and Soil group gets involved early with design analysis, developing bid packages and interviewing specialty trade partners when applicable. For existing buildings, especially historical ones, they perform in-the-field investigations to analyze specific elements like the roof structure, exterior enclosure, and potential tie-in points if it includes a new addition. This will ensure the structural infrastructure is in place to minimize any unforeseen obstacles during construction. The soil team studies the soil during preconstruction to recommend the best footings and support for the building.
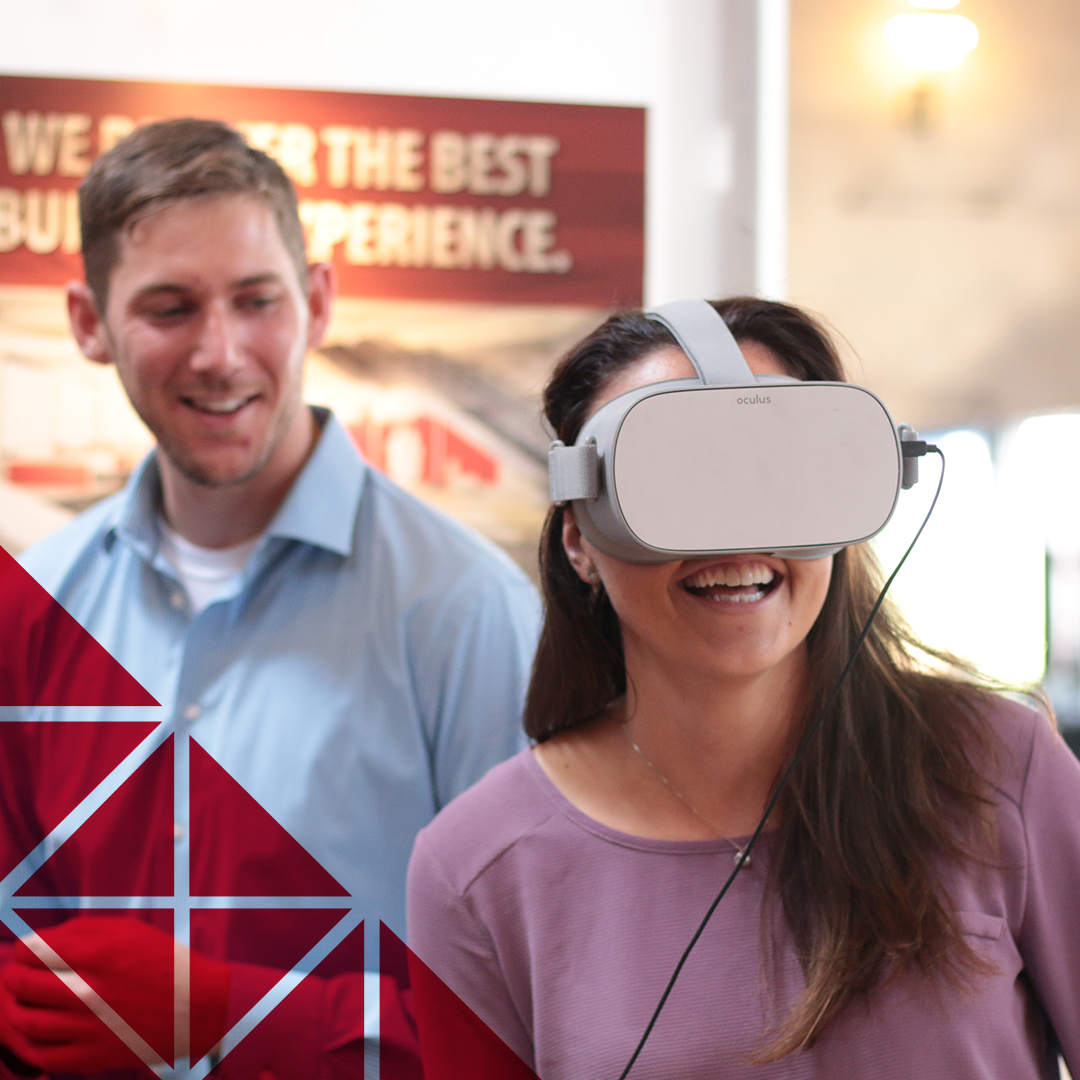
VDC
The VDC team is our technical liaison division in the Building Performance Solutions department. Their hallmark is clash detection where the team models to “build the building virtually” before we ever move dirt to manage risk with minimal impact. Coordination meetings identify the clashes and develop resolutions with trade partners before construction begins. Holding these virtual reviews increases the level of quality control early to reduce costly field conflicts later.
Virtual mock ups of complex portions of the project provide field operations additional details to determine how many trade partners are involved and the logistics behind assembly.
Laser scanning of an existing building creates millions of data points when there are no drawings available, which provides a field-accurate model where nothing existed before.
In-wall photography documents what’s behind a wall from start to finish. This technology lets you hold up an iPad to the wall and see the hidden duct work and conduit.
Our VDC department researches and tests the latest emerging technology to bring the best options to our clients for a better building experience. Then they share that technology with owners, architects, engineers and trade partners to maximize efficiencies for project success.
These advanced digital tools add value throughout the entire project timeline; reducing cost, time and waste, while improving efficiency and quality.
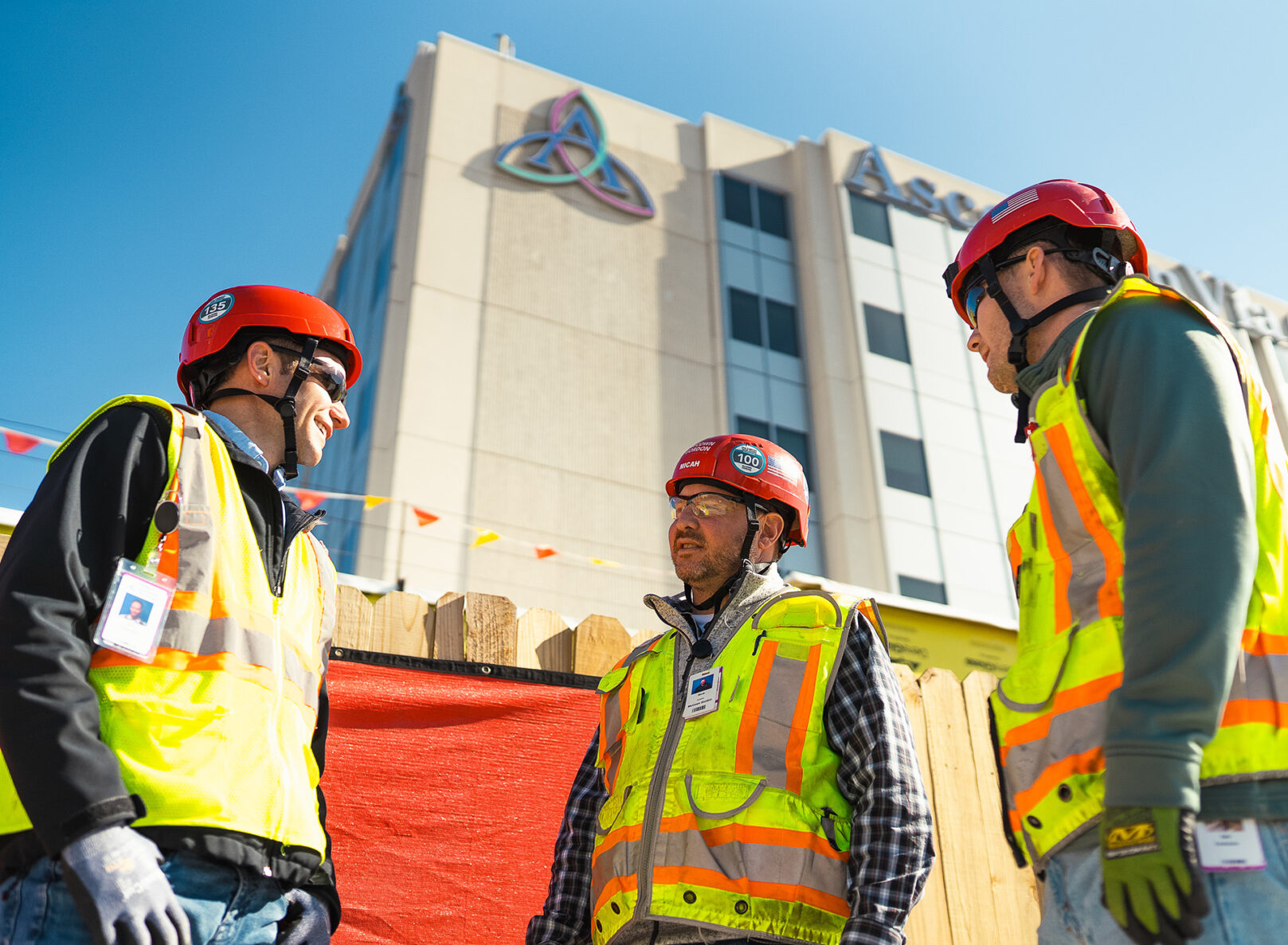
qa/qc
The Quality Assurance and Quality Control (QA/QC) team proactively manages project quality through early reviews, trade partner engagement, strict enforcement and dogged follow up. Quality is an integral part of how we perform, which results in more long-lasting facilities with fewer changes during construction.
Quality control begins with proper planning at the design phase and ends with acceptance of installed assemblies. Our quality planning tools include establishing the specification and acceptance criteria, and plan review. During the bidding and construction phases, McCownGordon manages quality closely through bidder qualification, shop drawing review, permit acquisition and pre-installation meetings. This process continues into construction to ensure quality expectations are met and exceeded.
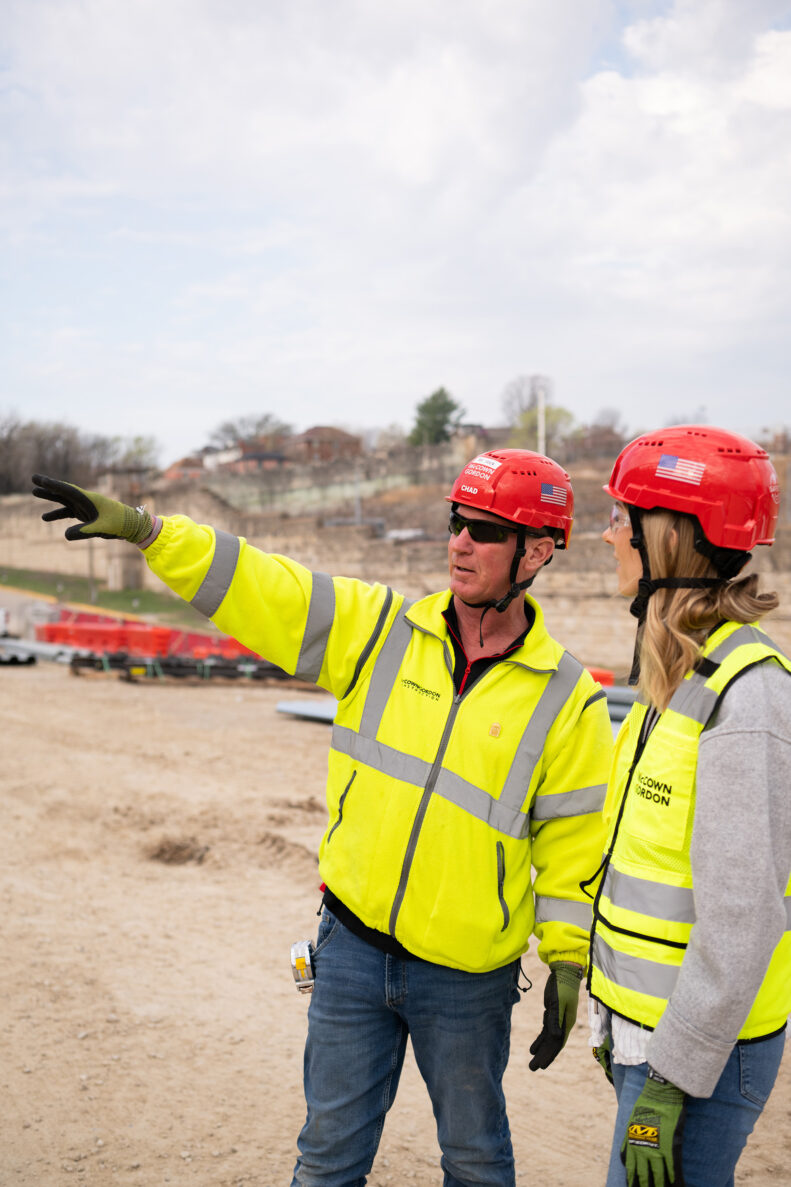
SUSTAINABILITY
Our team evaluates the building and site early during preconstruction in order to reduce the environmental impact of practices and materials and focus on life cycle assessments (LCA). We use the latest technology to quickly evaluate energy usage versus utility, maintenance, and replacement costs to provide our clients the most sustainable option.
At the start of construction, we implement a strict site management plan which reduces erosion, heat island effects and construction-related pollution. We prioritize the management of construction waste and identify certain materials that can be salvaged or recycled and track them. Following LEED practices, we evaluate LCAs on materials to address renewable and recycled-content solutions. Our in-house sustainability team assists in validating energy and water-efficient systems, fixtures and controls sequences ranging from ground source heat pumps, LEDs and grey water systems to variable refrigerant flow systems and low-flow fixtures.
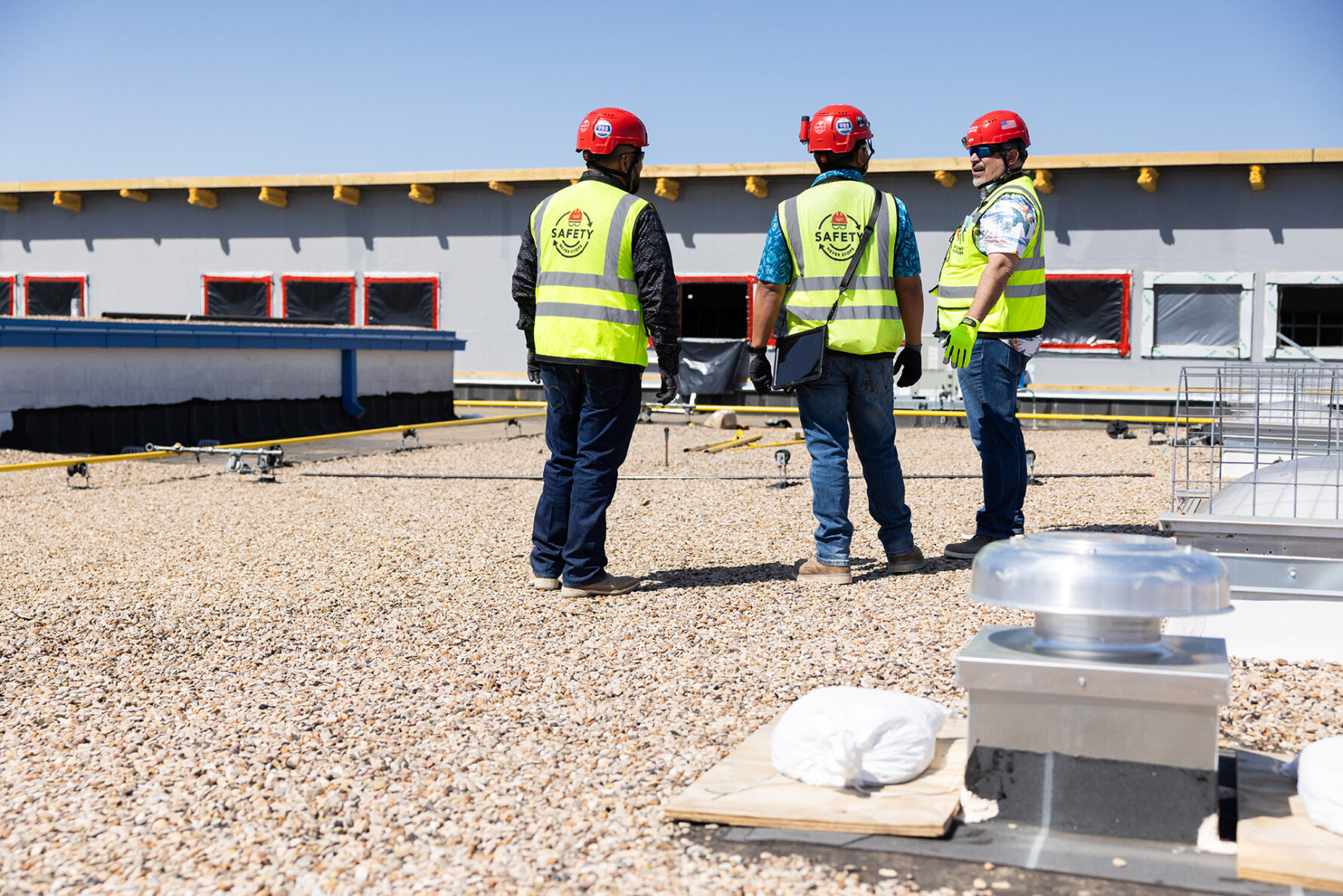
Our building performance solutions team can set your project apart.
Let us show you how we can add value to your project.
Our Services
From Our Experts
Ready to Start Your Project?
We would love the opportunity to show you how we can bring your vision to life.
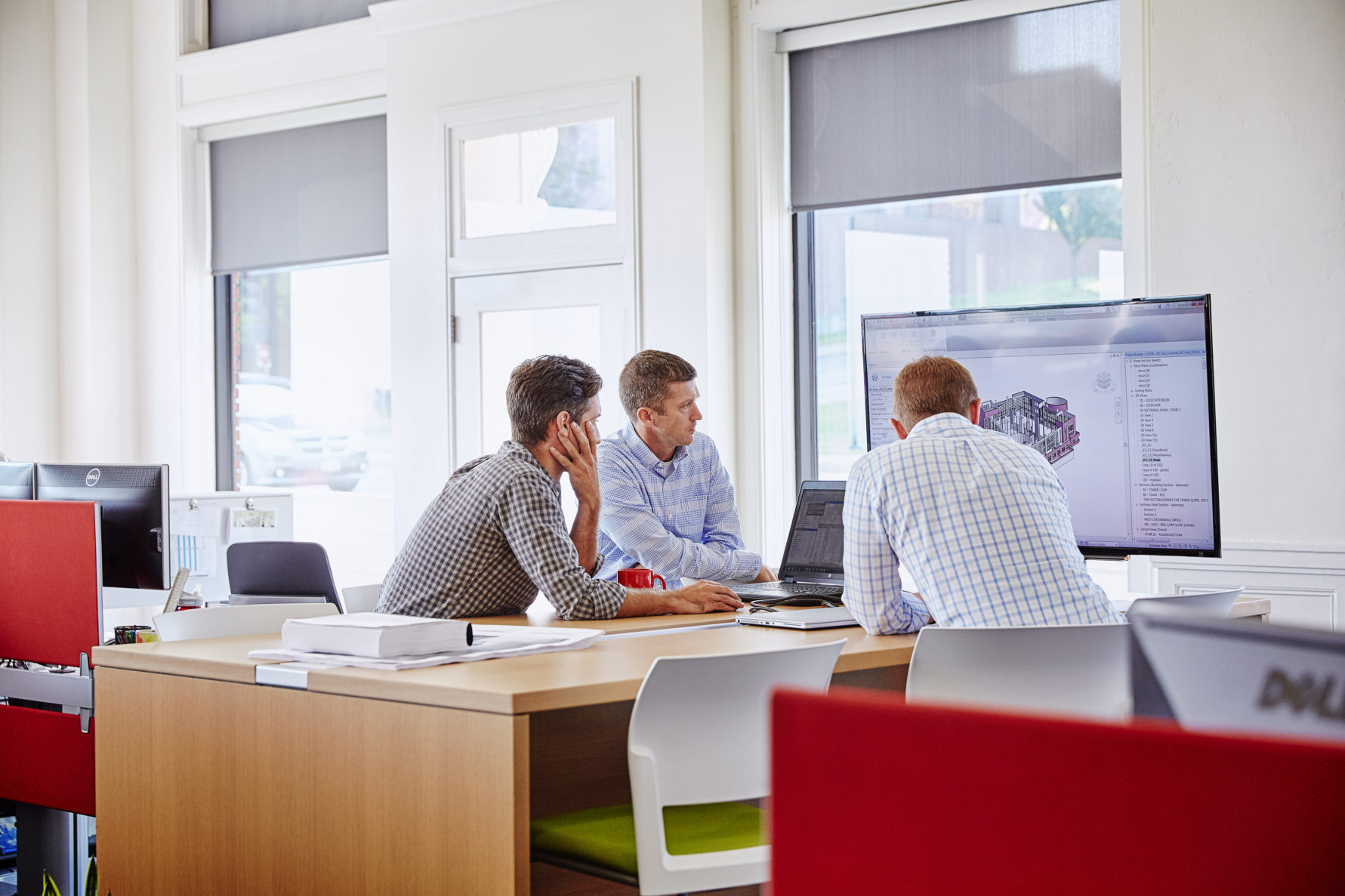
The first thing we build is relationships.
We’d love to learn more about your needs or upcoming project to help bring your vision to reality.