Enhanced manufacturing services: laser scanning
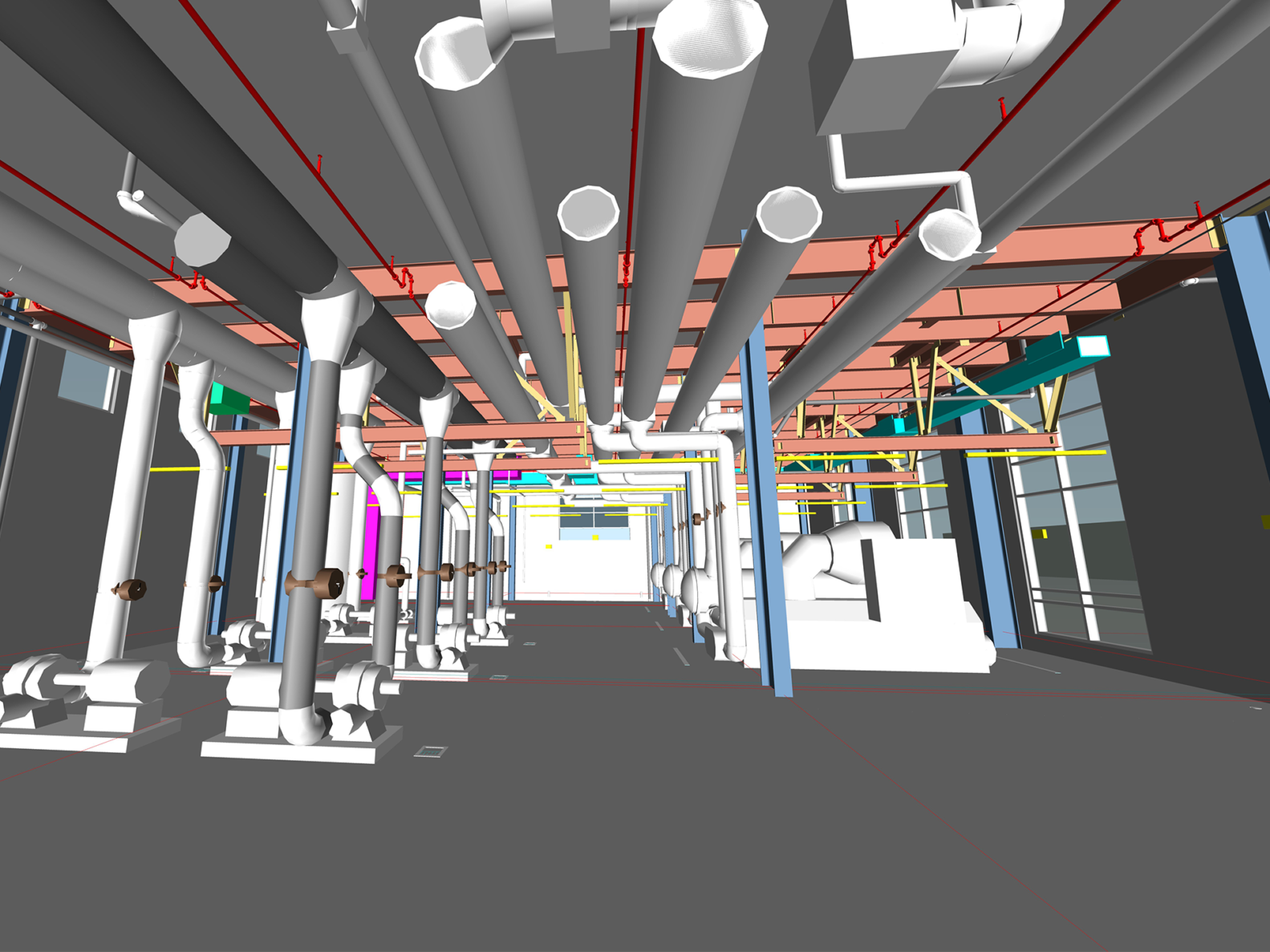
Manufacturing facilities are complex spaces. Every inch on a plant floor is maximized to create the perfect environment for fabrication. And when machinery is intricately arranged to maximize production it’s extremely important to accurately capture locations. Capturing these data point locations helps owners understand what space is available for future production expansion or modification. Having this at their fingertips allows all stakeholders make quicker decisions saving time and money.
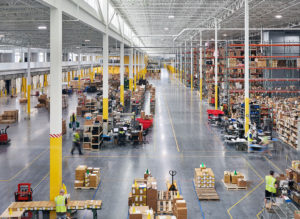
Within these tight spaces using manual measuring tools like tape measures isn’t feasible. These outdated methods often produce inaccurate measurements and are too laborious in tight manufacturing spaces. Our virtual technology team has taken this drive for accuracy to the next level. We regularly implement laser scanning technology to produce 3D models of manufacturing facilities for our clients. These 3D laser scans can produce photo-realistic as-built drawings accurate to the 1/16 of an inch. Our clients use these precise files for coordination, record-keeping and accurately capturing photo-realistic geometry of a specific space.
Millions of data points come together in a photo-realistic image that compose these data-rich models. From there, our teams can create 3D models for our clients to visualize their spaces.
By analyzing these scans and models, our teams can help reduce construction costs and operational costs. Our in-house engineering department works with clients to dive into the virtual models to maximize construction efficiencies during design. Manufacturing system engineers can work with our clients’ operations teams to ensure the space is working the most efficiently.
By providing the exact dimensions for large-scale complex projects we can help develop scopes in the preconstruction process. A laser scan helps the preconstruction and design team with a large amount of data points centered around obstructions pushing them to analyze and investigate other paths and design possibilities to avoid them. Ultimately, it reduces the risk of not knowing what’s ahead and helps save time by identifying scopes earlier in the process.
Whether it is a food and beverage facility, consumer products or pharmaceutical production facility, the need for accurate as-built drawings is paramount. Contact us learn more on our virtual design and construction capabilities and how they can increase your ROI.
Case study:
At South Dakota State University in Brookings, South Dakota our VDC team scanned the facility to determine the best location for the new chiller piping to tie into the existing chiller piping, which would impact where the other trades’ systems would be placed in order to avoid clashes with one another. We knew the general locations, but if the new piping were to be off by a few inches, it could create field installation issues with other trades’ systems in the new portion of the chiller plant.
We captured 3D laser scans of the existing chiller plant to determine all the locations and sizes of the existing chiller piping. We then uploaded the laser scans to our software, processed the data, and imported the scanned imagery into our coordination model, which also contained the trades’ coordination models. From there, our VDC team took measurements between the new piping models and the scanned imagery of the existing piping to determine the exact dimensions the plumbing detailer needed to adjust their model content. Once the team had aligned the new and existing piping, we completed clash detection with the other trades in the chiller addition.
Ultimately, if this additional coordination step was omitted from the process, there would have undoubtedly been numerous coordination issues in the field. By using this advanced technology our team reduced clashes and saved the university time and money.
Follow Us
McCownGordon strives to be a thought leader in our industry and provide continuous insight and updates to our clients to ensure we're keeping up with the latest technology and safety standards and regulations.
Sign Up